MTB Handlebar Testing
- Posted on
- By Fair Wheel
- Posted in Tech
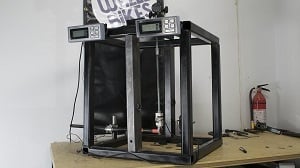
In the past year we've done deflection testing on cranks, stems and road handlebars. Now it's time to introduce the Mtb handlebar testing. For this first round of testing we've tested 50 different handlebars. While each model may not be unique each one does have unique characteristics. For example we may have tested the same bar in different lengths to see how length affects stiffness. We also looked at this with some rise and sweep options as well as different materials.
We’ve once again brought back our favorite engineer, Jason Krantz. Jason’s a mechanical engineer whose graduate work focused on the intersection of composite materials and finite element analysis. Jason has worked for several companies in the bicycle industry and never fails to amaze us with the depth of his cycling related knowledge. He adds real value to all of the tests we perform.
Disclaimer: A lot of typing and numbers have gone into this article and we apologize in advance for any typos, but would warn that the possibility of mistakes is present.
Why do deflection testing on bars?
We don’t believe that there is any meaningful efficiency (speed) to be gained through a stiffer handlebar, so why test for that? Losses in efficiency are minimal but a stiff handlebar and stem can make the bike feel more responsive to rider inputs, especially out of the saddle and with suspension. For road handlebars we wrote, "We’re unconvinced of any performance benefit to a stiffer bar, but many people like the feeling one provides. What we are convinced of is that the additive effect of parts that deflect more does at some point become a problem. The point at which it becomes a problem is different for different riders and terrains. " There is clearly a line for a given rider in a given set of circumstances where too much flex becomes a problem and inhibits steering and tracking on technical terrain. It may be worth noting here that one major manufacturer declined to be included in the testing by stating that they don't design their bars to be stiff they design them to be comfortable. While this may be applicable with road bars, we have to politely disagree when it comes to mtb bars on front or fully suspended bikes, we feel that intentionally adding flex is not a desirable trait. If one were designing for fully rigid bikes then that would be a different matter.
If you combined a very flexible, frame, steerer, stem, bar etc… into one bike you’d more than likely notice it in it’s handling. If you mounted the most rigid pieces you could find in one bike you likely would have more than adequate stiffness but at the same time perhaps some un-necessary weight gain. The ideal is some moving sweet spot in between that is different for each given set of circumstances. Hopefully through continual updates to this list and the stem tests, we can provide the information that helps riders find the sweet spot in both bar and stem that each one individually desires.
About the Testing Method
Each handlebar was mounted in the fixture and the testing performed 3 times and then averaged. All bars tested were loaded 1cm in from the end of the bar. Each bar was mounted with recommend torque specs and preloaded with 20 pounds of force. Once preloaded the equipment was zeroed and another 50 pounds of force was added and a measurement recorded. The measurement was taken at the point of load
Notes about the loads tested: The actual load doesn’t matter because the response of the structure is linear. That is, a handlebar that deflects 5mm under a 25-lb load will deflect 7.5 mm under a 75-lb load, 10 mm under a 100-lb load and so forth. This assumption of a linear response to loads is valid roughly until an aluminum bar bends permanently (plastic deformation) or until a carbon bar breaks (brittle failure). These bars were loaded with 50 pounds because it’s a nice round number and a fairly realistic approximation of real-world xc conditions.
If a sprinting rider is pushing on the left pedal with 200 lbf (in other words, he can squat 400 lbs), he must create an equal and opposite moment (twisting force) via the handlebars. The pedal is about half as far from the frame centerline as the handlebar is, so it would take a reaction force of 100 lbs at the right-hand bar to counteract the pedaling force. This is the same as applying 50 lbf up on the one side of the bar and 50 lbf down on the other; the total moment is the same.
Stiffness to weight ratio: This was calculated using =((1/avg. defl) / weight) * 2000
Notes about rise and sweep: We tested and compared bars with a range of rises and sweeps. All rise and sweep numbers were provided by the manufacturers.
Carbon Fiber vs. Aluminum: While carbon offers little or no weight savings when applied to stems (see our previous stem test), the lightest handlebars are usually made from laminated fiber. Handlebars are stressed primarily in bending, and 0-degree carbon fibers take these loads very, very well. When you throw in a few layers at 45 degrees to deal with torsional loads and maybe some circumferential reinforcements where the levers mount, you often end up with a bar that’s a bit lighter than the equivalent aluminum bar, but often more expensive.
As noted above, aluminum bars tend to fail by bending permanently (ductile failure) while carbon bars usually snap into pieces (brittle failure). While “shattered” carbon bars make for shudder-inducing post-crash photos, keep in mind that a strong carbon bar will shrug off loads that would bend its aluminum counterpart. Ductile failure is not necessarily a better failure mode than brittle failure.
Reduced weight is a wonderful thing, but do carbon bars offer another advantage: Composite structures generally damp vibration better than metallic ones, and many riders have found real-world damping benefits when they fit a carbon handlebar, though arguably this may apply more to road than a mountain bike, especially when suspension is considered .
Notes on Sweep: Sweep seems to have no measurable affect on deflection. Take the Thomson Ti bars for example, we tested two flat bars one with 6 degree and one with 12 degree sweep, but both with the same length and very similar weights. The result was that both bars had near identical deflection and stiffness to weight.
Notes on width: This review covers a lot of bars with different intended uses, the first segment is 50 handlebars in widths varying from 560 to 800 mm. Width seems to be one of the most critical components, not only in rider preference but also in a bars performance in this test. Longer bars have to be heavier not only due to their added length but also to reduce the deflection under load. This leads to short bars having a definite advantage in deflection testing, weight and stiffness to weight. Therefore we've broken the test up and will compare results by groups based on 50mm increments. We feel this is a better way to present the results as most riders have an ideal width but can vary up or down from that a little without bother.
On to the test results:
Group 1: 560mm-600mm
Manufacturer | Model | Width | Deflection | Weight (g) | Stw | Rise/Sweep | Material | Wt per cm | Price |
---|---|---|---|---|---|---|---|---|---|
Schmolke | TLO | 560 | 4.165 | 80.0 | 6.00 | 0mm/6deg | Carbon | 1.43 | $323 |
Mcfk | UL Flat | 580 | 4.06 | 104.3 | 4.73 | 0mm/6deg | Carbon | 1.80 | $219 |
New Ultimate | 580 XC | 580 | 5.72 | 96.8 | 3.62 | 0mm/5deg | Carbon | 1.67 | $165 |
Far and Near | Flat Al | 600 | 5.88 | 124.0 | 2.74 | omm/8deg | Alloy | 2.07 | $60 |
Kcnc | Rampant | 600 | 4.69 | 184.4 | 2.31 | 0mm/6deg | Alloy | 3.07 | $60 |
Kcnc | SC Bone | 600 | 5.32 | 124.5 | 3.02 | 0mm/5deg | Alloy | 2.01 | $70 |
New Ultimate | Scandium | 600 | 5.54 | 116.3 | 3.11 | 0mm/5deg | Alloy | 1.94 | $80 |
Group 2: 610-650mm
Manufacturer | Model | Width | Deflection | Weight (g) | Stw | Rise/Sweep | Material | Wt per cm | Price |
---|---|---|---|---|---|---|---|---|---|
New Ultimate | R620 | 620 | 5.83 | 131.4 | 2.61 | 30mm/8deg | Carbon | 2.12 | $180 |
Race Face | Next SL | 625 | 6.01 | 131.5 | 2.53 | 5mm/7deg | Carbon | 2.10 | $150 |
Enve | Sweep | 640 | 5.42 | 123.2 | 2.99 | 0mm/9deg | Carbon | 1.93 | $160 |
Mcfk | UL Flat | 640 | 5.79 | 109.1 | 3.16 | 0mm/6deg | Carbon | 1.70 | $219 |
Schmolke | TLO | 640 | 5.95 | 82.1 | 4.09 | 0mm/6deg | Carbon | 1.28 | $323 |
Truvativ | T40 | 640 | 5.34 | 158.3 | 2.37 | 15mm/9deg | Carbon | 2.01 | $140 |
Group 3: 660mm-700mm
Manufacturer | Model | Width | Deflection | Weight (g) | Stw | Rise/Sweep | Material | Wt per cm | Price |
---|---|---|---|---|---|---|---|---|---|
Control Tech | Ti-Mania | 660 | 5.67 | 225.0 | 1.57 | 0mm/5deg | Titanium | 3.41 | $150 |
New Ultimate | Scandium Low | 670 | 5.84 | 180.2 | 1.90 | 10mm/5deg | Alloy | 2.69 | $90 |
Ritchey | WCS Carbon | 670 | 5.78 | 189.7 | 1.82 | 15mm/9deg | Carbon | 2.83 | $160 |
Schmolke | TLO Low | 670 | 6.48 | 107.0 | 2.87 | 15mm/7deg | Carbon | 1.60 | $371 |
Schmolke | TLO | 680 | 8.8 | 89.4 | 2.54 | 0mm/6deg | Carbon | 1.31 | $323 |
Box | XBar XC 35MM | 700 | 5.68 | 163.8 | 2.15 | 6mm/6deg | Carbon | 2.34 | $129 |
Extralite | Hyperbar | 700 | 9.01 | 103.3 | 2.15 | 5mm/6deg | Carbon | 1.48 | $210 |
Mcfk | UL Flat | 700 | 7.45 | 138.7 | 1.94 | 0mm/6deg | Carbon | 1.98 | $219 |
Mcfk | UL Flat 9 | 700 | 7.42 | 121.7 | 2.22 | 0mm/9deg | Carbon | 1.74 | $252 |
Mcfk | UL Low | 700 | 7.70 | 125.4 | 2.07 | 15mm/6deg | Carbon | 1.79 | $264 |
Promax | CB1 | 700 | 5.36 | 174.6 | 2.14 | 6mm/6deg | Carbon | 2.49 | $100 |
Group 4: 710mm-750mm
Manufacturer | Model | Width | Deflection | Weight (g) | Stw | Rise/Sweep | Material | Wt per cm | Price |
---|---|---|---|---|---|---|---|---|---|
Kcnc | SC Rise | 710 | 6.34 | 241.1 | 1.31 | 15mm/8deg | Alloy | 3.40 | $70 |
Alchemist | Carbon | 710 | 6.93 | 127.1 | 2.27 | 0mm/9deg | Carbon | 1.79 | $235 |
Control Tech | Titanium | 720 | 6.13 | 277.5 | 1.18 | 0mm/9deg | Titanium | 3.85 | $165 |
Ritchey | Trail | 720 | 6.74 | 239.1 | 1.24 | 5mm/9deg | Alloy | 3.32 | $75 |
Thomson | Titanium | 730 | 5.69 | 315.9 | 1.11 | 0mm/6deg | Titanium | 4.33 | $250 |
Thomson | Titanium | 730 | 5.70 | 316.4 | 1.11 | 0mm/12deg | Titanium | 4.33 | $250 |
3T | Extendo Pro | 740 | 8.59 | 276.4 | 0.84 | 31mm/12deg | Alloy | 3.74 | $75 |
Enve | DH (Cut) | 740 | 5.91 | 217.6 | 1.56 | 23mm/9deg | Carbon | 2.94 | $175 |
Enve | Rise | 740 | 7.18 | 191.6 | 1.45 | 23mm/9deg | Carbon | 2.59 | $160 |
Enve | Sweep | 740 | 7.57 | 171.5 | 1.54 | 0mm/9deg | Carbon | 2.32 | $160 |
FSA | Gradient Gravity | 740 | 6.69 | 204.9 | 1.46 | 15mm/9deg | Carbon | 2.77 | $230 |
Extralite | Hyperbar | 750 | 10.37 | 108.0 | 1.79 | 5mm/6deg | Carbon | 1.44 | $210 |
Tune | Turnstange Flat | 750 | 10.06 | 113.9 | 1.75 | 0mm/6deg | Carbon | 1.51 | $239 |
Tune | Turnstange Rise | 750 | 10.29 | 121.7 | 1.60 | 15mm/5deg | Carbon | 1.62 | $239 |
Group 5: 760mm-800mm
Manufacturer | Model | Width | Deflection | Weight (g) | Stw | Rise/Sweep | Material | Wt per cm | Price |
---|---|---|---|---|---|---|---|---|---|
Box | X-Bar Trail (35MM) | 760 | 7.04 | 181.8 | 1.56 | 15mm/7deg | Carbon | 2.39 | $139 |
Promax | CB-1 | 760 | 6.96 | 193.1 | 1.49 | 15mm/7deg | Carbon | 2.54 | $100 |
RaceFace | Next Carbon (35MM) | 760 | 6.60 | 182.6 | 1.66 | 10mm/8deg | Carbon | 2.40 | $150 |
Race Face | Turbine (35MM) | 760 | 6.99 | 265.1 | 1.08 | 10mm/8deg | Alloy | 3.49 | $80 |
Race Face | Turbine (35MM) | 760 | 6.88 | 268.5 | 1.08 | 20mm/8deg | Alloy | 3.53 | $80 |
Box | X-Bar Trail (35MM) | 780 | 9.37 | 186.5 | 1.15 | 30mm/9deg | Carbon | 2.39 | $139 |
Promax | CB-1 | 780 | 9.03 | 209.9 | 1.06 | 30mm/9deg | Carbon | 2.69 | $100 |
Race Face | SixC | 785 | 7.55 | 225.9 | 1.17 | 20mm/8deg | Carbon | 2.88 | $160 |
Box | X-Bar DH (35MM) | 800 | 7.69 | 230.6 | 1.13 | 15mm/7deg | Carbon | 2.88 | $149 |
Box | X-Bar DH (35MM) | 800 | 7.47 | 249.4 | 1.04 | 30mm/9deg | Carbon | 3.12 | $149 |
Enve | DH | 800 | 8.10 | 240.5 | 1.03 | 23mm/9deg | Carbon | 3.01 | $175 |
Race Face | SixC (35MM) | 800 | 7.46 | 208.1 | 1.29 | 20mm/8deg | Carbon | 2.60 | $170 |